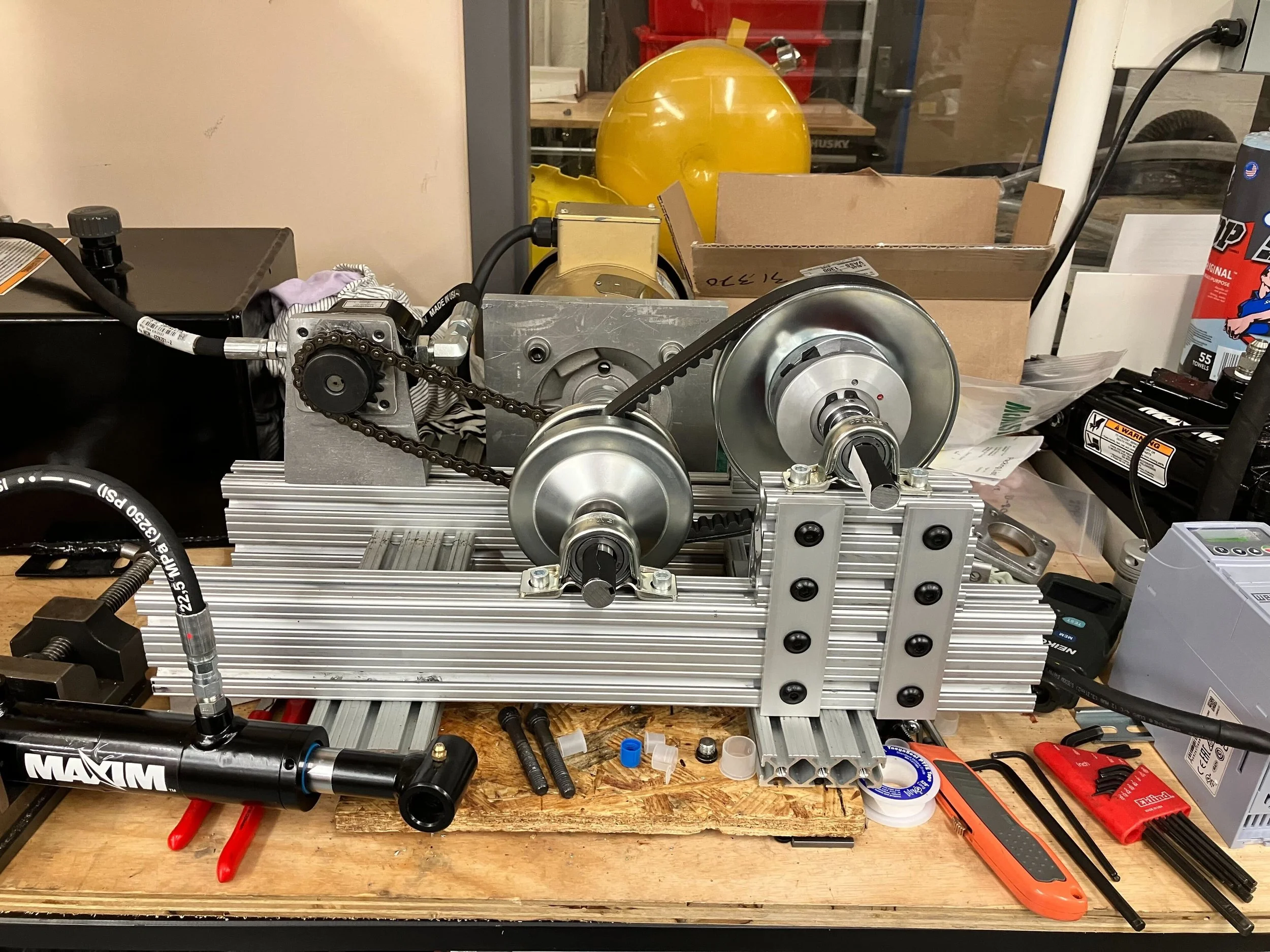
Fall 2023, MIT
Motorcycle Tractor Hydraulic Decoupling Project
Scroll ↓
Decoupling the Hydraulic and Drive Systems on a Motorcycle Tractor
My lab invented a motorcycle tractor by adding farming features onto a AWD motorcycle including a hydraulic system to use with farming attachments such as a plow. However, the hydraulic pump was downstream of the clutch which resulted in the hydraulic system being inoperable if the motorcycle was in gear and not moving. In this project, I proposed a design modification always maintain hydraulic power regardless of the drive state, and I produced a design spreadsheet guide the implementation of this modification in future iterations of the motorcycle.
Background
A hydraulic pump was installed onto the motorcycle near the transmission. However, the clutch is incorporated in the torque converter by the engine. This results in the hydraulic pump only getting power when the clutch is engaged, which does not happen if the motorcycle is in gear and not moving.
Proposal
I proposed that we power the hydraulic pump directly off the driveshaft before the clutch, so it has power whenever the engine is running.
Analysis
I drew up free body diagrams to ensure that this new configuration would not add more stress to the driveshaft than what it already experienced. By placing the pump opposite the transmission, it actually reduces stress on the driveshaft while running.
Experiment
I built a mockup of the proposed system to ensure that we would maintain hydraulic power regardless of the drive state, thus ensuring the proposal would function.
Design Spreadsheet
I compiled all the theory I developed into a design spreadsheet that future users can leverage to test different design parameters on the next generation tractor. The user can quickly test different angles and distances and see if the resulting forces are acceptable for the engine.